Robotics Research
Georgia Institute of Technology
Complex Rheology And Biomechanics Lab
The CRAB Lab researches problems in non-equilibrium systems that involve complex materials and granular media that can flow when stressed. For example-- how do organisms like lizards, crabs, and cockroaches move their bodies to overcome obstacles like sand, bark, leaves, and grass? The CRAB Lab integrates laboratory and field studies of organism biomechanics with laboratory studies of physics of the substrates, models of the substrates, and mathematical and robotic models of the organisms to answer these questions.
Projects
Modeling General Relativity with Deformation-Induced Locomotion
Yasemin Aydin, Olivia Lofaro, Shengkai Li, Jennifer Rieser, Daniel Goldman
August 2016 – February 2017



Modeling General Relativity with Deformation-Induced Locomotion
Yasemin Aydin, Olivia Lofaro, Shengkai Li, Jennifer Rieser, Daniel Goldman
August 2016 – February 2017
Intro:
A mass depressing the center of an elastic membrane is often used as a classroom model to explain the forces of gravitational pull. Traditionally, a marble is used to represent a body with initial velocity. The marble is thrown tangentially onto the trampoline, and the marble orbits the central mass. This is a modification on the classic experiment with the added control variable of constant velocity in the orbiting body by using a robot rather than a marble.
About The Robot:
The robot is simple and lightweight; a single motor turns at a constant velocity. It is equipped with a differential drive system and passive markers that can be tracked as a rigid body by the optical camera setup above.
About The Test Bed:
Rather than varying the weight of the central mass to change the angle of depression, an actuator has been placed in the center of the fabric, and achieves the same warping effect on the material. There is a network of optical cameras above the experimental setup, and a matrix of passive reflective markers on the fabric. The cameras use these markers to map the deflection of the surface as the robot drives on top of it.
Skills Developed:
-
Test Bed Design
-
Dynamic Modeling
-
Perception Systems
-
MATLAB
-
Data Presentation

Smart Particles: Active Matter Particles
Will Savoie, Olivia Lofaro, Daniel Goldman
May 2016 – August 2016
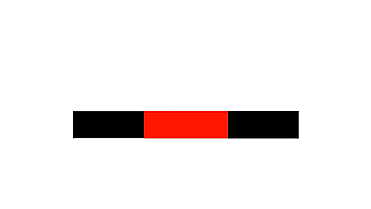


Intro:
Active matter is material composed of multiple active particles, each of which move independently to form a cohesive group of forces. These particles seen to the left can be manipulated into a straight line or a ‘U’ staple shape by playing different sound frequencies over a speaker. The position is dependent on the frequency of the tone. A doctoral candidate in the CRAB Lab developed these robots and has been conducting clogging experiments with them.
About The Robot:
Each Smart Particle is controlled by an onboard Arduino Mini and powered by a collection of solar panels attached to the wings. The majority of the wiring is done through a printable circuit board affixed to each particle.
About The Test Bed:
These particles are deposited into the tilt table test bed shown below and are analyzed through different flow and clog experiments. The robots are manipulated as they fall through a funnel. When the experiment is complete, the funnel is reversed and the table is tilted in the opposite direction, allowing the experiment to reset with zero human interaction. This allows experiments to be run continuously.
Skills Developed:
-
Test Bed Design
-
PCB Manufacturing
-
Arduino
-
Machine Shop
-
C++
All-Terrain Mudskipper Robot
Olivia Lofaro, Daniel Goldman
May 2015 – May 2016
Intro:
The mudskipper is uniquely adapted to locomotion over a variety of surfaces with an otherwise minimal feature set. In my project, I investigated the effectiveness of this flipper motion through a robotic physical model. Every iteration of the robot was tested on both land and granular material, and then upgraded based on the success or failure of the motion.

Generation 1:
The original iteration the robot had a 3D printed body, shoulder joints that allowed motion on 2 axes, and an onboard Arduino Mega. The drawbacks of the design were the cardboard flippers and the lack of a tail. There was little to no control implemented in the code; the wings jerked in a swimming motion. This design was a crude primary version of the robot I planned to eventually develop. Its purpose was to test the mechanical aspects of my design, which proved effective. Motion through granular material was relatively successful, however locomotion on solid ground was a total failure.

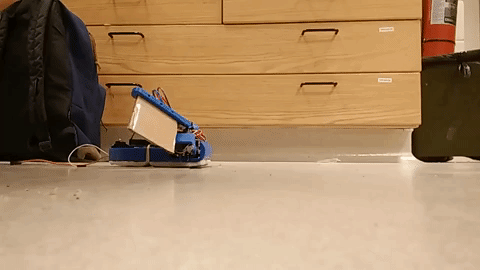

Generation 2:
The second iteration was slightly more advanced; the cardboard flippers were replaced with sheets of hard plastic with rubber flipper tips attached to the end to improve traction. The control began to utilize the servo’s analog feedback sensing so the microcontroller could determine if it had reached the position it was intending to send the flipper, and a tail was added. The progression of the robot through the granular material remained successful, and was much more controlled. Locomotion on hard ground also became possible with the added friction caused by the rubber tips on the flipper and the lift contributed by the tail. The addition of a tail also allowed for more advanced behaviors such as turning. Turning was successful in both granular material and on solid ground. Interestingly, the robot pivots on a near-central axis when it turns, which is an advantageous feature because it minimizes the turning radius and the necessary space required to rotate.

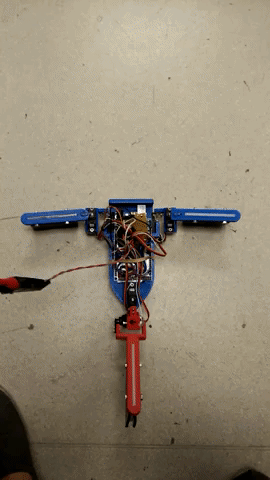
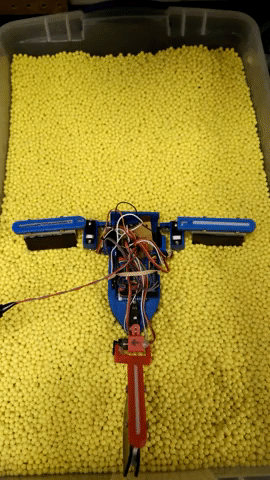

Generation 3:
The most updated generation of my mudskipper robot features double jointed connections at each servo motor. These reinforced contacts reduced the amount of unwanted movement in each flipper which was a large source of error in the previously conducted experiments. The code running on this generation allowed for synchronized and controlled flipper motion and featured obstruction detection. Instead of continuously pushing forward, the servos would attempt to overcome an obstacle for a certain period of time before giving up and continuing the cyclical flipper motion. The result was a robot that could clamber over a variety of materials. In experiments, the robotic mudskipper effectively moved through granular material and over cotton balls and through foam obstacles.
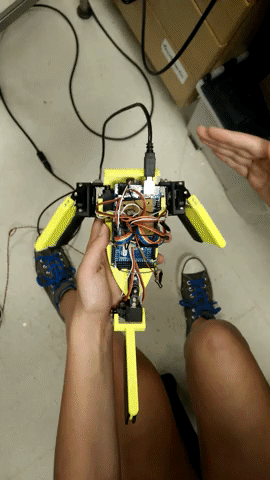
Skills Developed:
-
PID Control
-
Arduino
-
SolidWorks
-
3D Printing
-
C++
-
Circuit Design
-
Power Supply Design
-
Soldering
-
Project Management
-
Technical Writing
-
Data Presentation
-
Public Speaking
Robotic Ant Swarm Theory
Vadim Linevich, Olivia Lofaro, Daniel Goldman
January 2015 – May 2015
Intro:
Swarm theory applies the biological model of multiple simple workers all working to complete a singular task, as observed in some insect colonies such as termites or fire ants. This study focused on replicating the tunnel building behavior of fire ants. I assisted a Master’s student in improving and assembling a fleet of ant robots to mimic swarm behaviors.
About The Robot:
Each robot was fitted with an Arduino Mega, a Pixy camera, and multiple hand-soldered circuits. The camera would search for the “pheromone trail”, represented by a strip of pink tape leading to the tunnel. The robot would follow the line, and arrive at a cotton ball pile. The gripper would grab at the pile until it secured a cotton ball, and then the ant would turn around and exit the tunnel. At the end of the tunnel, it would deposit the cotton ball over the ledge into a bucket where the amount of mass moved could be recorded. Experiments were conducted over a variety of conditions and evaluated to see which swarm behaviors were most efficient.


Skills Developed:
-
Dynamic Modeling
-
PID Control
-
Perception Systems
-
Arduino
-
Solidworks
-
3D Printing
-
C++
-
Circuit Design
-
Soldering